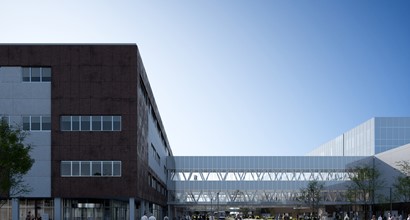
This is a translation of a danish article published in Hospital Drift & Arkitektur, Nytår 2020/2021, by Science Journalist Gordon Vahle, sciencejournalist.dk. If you want to read the article in danish you find it on page 22-24 on this link:
Interacting systems are crucial in hospital operations
Wonderware Scandinavia, authorized distributor of AVEVA Industrial Software solutions, specialises in systems that, ultimately, help hospitals deliver the right services, in the required quality, and at the right time. As the name implies, it is not only about solutions designed solely for hospitals. It is about managing processes and bringing systems together as one. Sales Representative Henrik Dybdahl Andersen from Wonderware Scandinavia puts it this way:
“Efficient hospital operations is basically about insight. Where is the equipment located? When? In what condition is it?” he says. This is, of course, a simplification. But it serves to describe some of the key demands to the solutions Wonderware delivers.
One example is a new logistics system and supply chain to Region Hovedstaden (the capital region of Denmark) following the decision to close down 10 Central Sterile Supply Departments (CSSDs) and replace them with two new, fully automated CSSDs. The two new CSSDs will provide all operating rooms in the region’s 10 hospitals with sterile instruments and other equipment, requiring a complete re-build of the logistics system from the ground up.
Another is a comprehensive system to integrate building management systems (BMS), manufacturing execution systems (MES), and a range of other systems at the new university hospital (Nyt OUH) in Odense, some 150 kilometres from Copenhagen, expected to open in 2023.
BMS – and more
Leveraging AVEVA’s extensive experience from the process industry, the new platform that will bring the systems at Nyt OUH together does not adhere to traditional boundaries within a hospital. After all, employees – whether they work in clinical care, building operations, logistics, medical technology, surveillance, service, administration, or any other function – are working to provide the best care possible to patients. So why should the systems controlling the processes be separated?
“They shouldn’t,” points out Henrik Dybdahl Andersen, who would in fact like to bring in even more aspects, such as booking and managing patient flow, into the platform. While that level of integration has not been reached just yet, Wonderware is still raising the bar with its solution for Nyt OUH.
Not only will BMS, HVAC, water, access control, lighting, fire alarm, sun blinds, etc. work together as one system; the entire logistics system is also connected, offering a complete overview of operating rooms, CSSD, elevators, AGV (Automated Guided Vehicles), track & trace of goods, manufacturing, pneumatic tube mail etc.
In other words: The dream of always knowing where things are at any given time is very nearly coming true.
Searching for items 20 % of the time
Why is complete control of everything crucial in a hospital? Henrik Dybdahl Andersen offers a relatively simple explanation:
“Studies show that there is a 20 percent time saving to be gained if everybody knows where everything is. Conversely, this means that employees spend one-fifth of their time searching for various items, ordering goods they thought were in stock, waiting for transport, getting the right systems up and running, etc.,” he says. “Running a hospital at its optimum performance requires a lot of moving parts, and the systems that make those parts move must also work together and communicate with each other. This is why BMS, MES, access control, booking systems, track & trace and everything else should ideally be connected via a common platform.“
An ordinary day in the operating room
AVEVA Industrial Software’s platform is widely used in complex process applications, including the pharmaceutical and chemical industries and food & beverage. But is also used in infrastructure, utilities, and other industries.
“We leverage our experience from these industries and apply them to the hospitals,” explains Henrik Dybdahl Andersen with an illustrative example: The preparation and logistics required for a surgical procedure.
The operation is booked via a booking system, initiating a requisition of the sterile utensils needed from the CSSD. These may be located in different places, may need to be sterilised, and must be picked up by an AGV or other robot.
Each packaging has an ID (chip or bar code) that shows when and where the item in question was sterilised, by chich autoclave and where and how it has been stored. On the day of the procedure, the operating room is heated to the required temperature in time for the patient and surgical team’s arrival. The same goes for pressure, temperature, ventilation, humidity, etc. The system has also performed a check to ensure that medical gases, lighting, power supply, and everything else are in perfect working order.
An AGV picks up the utensils, having already calculated the most passable route. If any obstructions have been put in its path, it is alerted by the planning system and will calculate another route. The AGV autonomously orders an elevator and makes sure others cannot use the elevator until the transport has reached the right floor.
Traceability detects errors in time
If any of these sub-processes do not happen at the right time and in the right place, the entire process is interrupted and delayed. Systems must be able to communicate even if the hospital uses different systems for building operations, booking, track & trace, surveillance, and so on. And it is precisely this communication the common platform handles.
“But it is in fact equally important that the system can interfere if something goes wrong. Traceability is paramount in hospitals and the pharmaceutical industry. With a system that – so to speak – is keeping tracks of everything, errors can be rectified before they progress and may have more severe consequences,” Henrik Dybdahl Andersen says, adding: “If an autoclave reports a failure or that there is a margin of error in the sterilisation process, you can recall and pick up only the utensils that were in that particular autoclave at that particular time. You won’t need to recall all other equipment that has been correctly sterilised on the day in question.“
Security is paramount
AVEVA’s platform could be compared to a railroad control centre. The system must tie together the various train stations – the operational IT systems – with each other and make sure that cargo and passengers – the data – are always delivered to the right place at the right time. However, while train stations are fairly easily connected given that railroad tracks are the same across most countries, things get slightly more complicated in the world of IT. IT systems are usually not designed for communicating with each other. Following our railroad analogy, this would be the equivalent of connecting the train stations with tracks of varying gauge, forcing the use of bogies at each station.
“In IT, communication between systems is usually enabled by making systems open. But that is a no-go for hospitals. Instead, we use encrypted connections to translate data from different systems to one common language,” explains Henrik Dybdahl Andersen.
With the entire hospital operation depending on communication between systems, extra focus has been put on security and reliability. Wonderware expects an uptime of at least 99,9 percent, not least due to double redundancy across the entire platform.
Human error is unlikely
“There is no human involvement in the daily planning, so the risk of human error is minimal,” Henrik Dybdahl Andersen points out.
It must, of course, be possible to adapt the system to changes. New systems can be added, and maybe an incident in one place must trigger other reactions elsewhere than initially planned.
Changing and adapting the systems is relatively easy because it is object-oriented and based on templates. This means that changes are automatically updated to all other relevant parts of the system, and the changelog ensures that documentation is always up to date,” says Henrik Dybdahl Andersen.
He emphasizes that the employees who will be working with the system will undergo extensive education. Training in the new system is already underway at Wonderware and as self-studies. It will be supplemented with thorough onboarding as the various parts of Nyt OUH are commissioned in 2023.
The AVEVA System Platform for bringing functions and systems together will have no impact on the ongoing work on existing operational IT systems for building management or others. But a number of new systems for managing AGV, pneumatic tube mail, track & trace etc., will be added – systems that are not used in the current Odense University Hospital.
If you have any questions regarding Nyt OUH and the AVEVA Solutions, click on the Contact button and we will get back to you as soon as possible. You can also contact our Sales Director, Peder Henriksen. Contact details to our offices you find in the Contact Us section.